II American Center
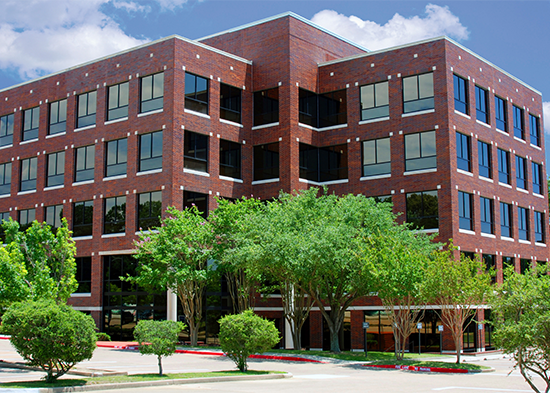
Facts
• 100k SF Class A suburban mid-rise
• Challenge: Aging HVAC infrastructure and equipment on
an early 1980s vintage building with extremely high
energy costs, numerous tenant complaints and failing
equipment resulting in high maintenance costs.
• The owner had been told that the entire system had to be
replaced because of age and condition at a cost of almost
$1 million dollars. This would entail a shut-down of each
floor for approximately one week while the existing chiller
AHU was removed and the new chiller AHU was
installed. Due to the building’s design, any new
installation would have equired a hole to be cut into the
curtain wall, the new unit to be cut into sections, crane
installation into the building via new curtain wall opening,
and re-assembly of the unit. Given the over 90%
occupancy of the building, this would have been very
disruptive to the tenants and extremely challenging to
manage. Working with an outside consultant, Younger’s
engineering and operations team developed a solution
that minimized downtime to the weekends only. They
determined that the existing system could be upgraded
instead of having to be replaced. The upgrades included
installation of new frequency drives, higher efficiency
compressors, and valves and controllers to interface with
the new building automation system. The resulting
solution cost less than $400,000, dramatically improved
temperature control and tenant comfort, reduced on-
going maintenance costs, and is projected to reduce
HVAC energy consumption by over 30%. This was all
accomplished with limited to no disruption to the tenants.
"We selected Younger Partners to
manage a 13 building portfolio
primarily because of their hands-on
leadership and the quality of the
property management team. From
accounting all the way through
operations, the transition was
expertly handled. Greg Grainger
and the Younger Partners team
absolutely delivered on their
commitments."
— Steve Mindlin
Mindlin Realty Advisors